Electrical Wiring
Unless you’re an experienced electrician, it’s advisable to leave this part of the project to professionals. However, you should know your needs and be in on the planning and supervision of wiring and lighting installation
As with the functional design of the workspace, a good electrical plan begins with a diagram. Knowing the location of your large pieces of electrically powered equipment, as well as your key workspaces, is vital in determining where best to place electrical outlets, dedicated circuits, receptacle heights, switch boxes, etc.
Larger pieces of equipment such as table saws should be powered via dedicated circuits. In one workshop, a 20-amp dedicated circuit was installed near the location where the table saw would later be placed. Each additional piece of large equipment also had a dedicated circuit. The outlet installed on each of these was a GFCI (ground-fault circuit interrupter) circuit. The GFCI receptacle is equipped with a measuring device that will shut down the power to the circuit immediately in the event of a short, reducing the possibility of electrical shock
Consider the total number of ordinary electrical outlets you’ll need, and keep in mind this rule of thumb: It’s hard to have too many outlets. In other words, people typically find that they eventually need more outlets than they first anticipated. In the case of our model workshop, nine receptacles were installed in addition to the dedicated circuits. The nine receptacles are in three circuits, with three receptacles on each circuit.
Consider also the best height for your receptacles. It may be beneficial to install workshop outlets higher on the wall than is typical in a home setting. This eliminates the problem of limited access to outlets when work surfaces or equipment are placed along the walls of the workshop. Higher outlets are also more convenient for plugging in and unplugging small power tools, which is something that happens frequently in a workshop.
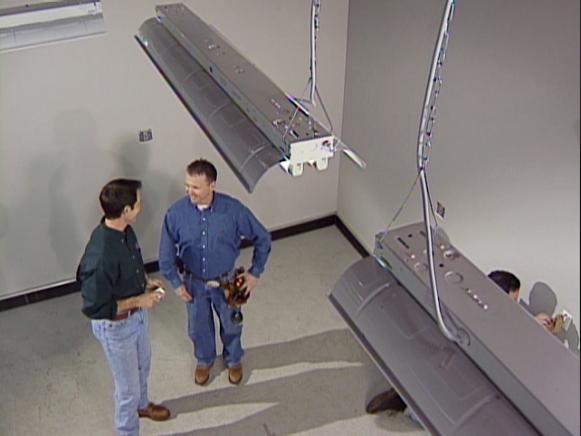
signs you should think about rewiring your home
Thirty-nine percent of home electrical fires involve outlets and receptacles, interior house wiring, and other electrical wiring. While these numbers are staggering, steps can be taken to prevent your home from becoming a statistic. The electrical system in your home may need to be repaired or updated. A complete rewire with a new electrical panel can be a big expense, but that pales in comparison to the importance of keeping your home and family safe.
Warning signs
An electrical system will often display signs when there are potential problems. If you notice any of these warning signs, have an electrician inspect your electrical system:
Frequent blown fuses or tripped breakers
An over-amped or over-fused electrical panel
Dimming or flickering lights, indicating the circuit is overloaded or has a loose connection
Hot or discolored switch plates, cords, or plugs
Light bulbs that frequently burn out in a socket, signaling a fixture that can’t handle the bulb wattage
Buzzing or sizzling sounds
A burning smell
Arcs or sparks from an outlet when you plug or unplug a cord
Loose outlets
Cracked, cut, or broken insulation
Electrical shock when you plug in or touch a cord
Other reasons to check the wiring
Even if you don’t notice any warning signs of faulty wiring, it’s a good idea to have your home’s electrical system inspected periodically. Electrical codes vary depending on where you live, but there are common situations that warrant an inspection from a qualified professional.
If your home is more than 40 years old
If you’re relying on extension cords for power
If you’ve made major home improvements or added major new appliances that could strain your existing system
If your home has ungrounded, two-prong outlets
If your home has aluminum instead of copper wiring
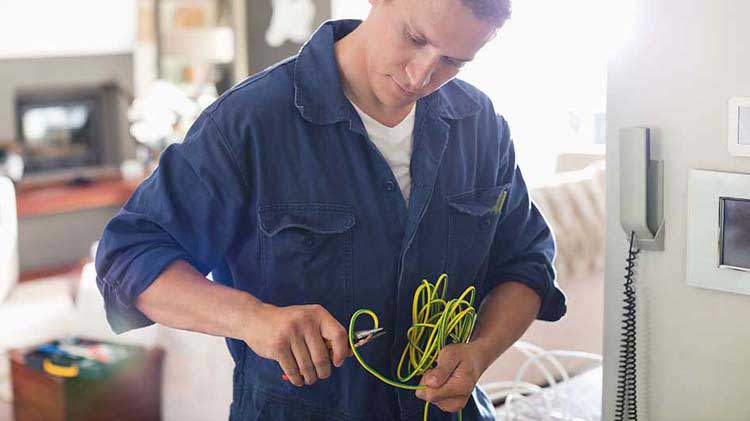
Aluminum wiring
The last time you looked for a new home, you probably had a shopping list: three bedrooms, two bathrooms, fireplace, lots of storage space. You probably didn’t give the in-home wiring a second thought. As long as you can plug something in and it works, it’s all good, right? Not necessarily. If your home has aluminum wiring, you could be in trouble in more ways than one.
What is aluminum wiring?
Aluminum wiring, though not used anymore, was once considered a safe and inexpensive alternative to copper. Copper wiring is really the wiring of choice, but for a while, approximately between 1965 and 1974, copper was so expensive that everyone was looking for a way to cut costs when wiring a home. And voila, aluminum wiring was the answer. However, it didn’t take long (about a decade) to discover that aluminum wiring tended to become defective much more rapidly than copper. In fact, if left neglected, a serious fire hazard could be lurking in outlets, light switches, or fixtures, as the electrical connections cause overheating in the wiring.
How does aluminum wiring work?
Aluminum wiring works the same way regular copper wiring works, but there is a significant problem which has made aluminum a thing of the past, when it comes to wiring homes for electricity. The main danger with this wiring is in the connections. When electricity passes through electrical cables and connectors, the wires expand and heat up. One of the issues with this type of wiring is that it expands three times more than copper does. In other words, it has a much higher rate of thermal expansion. When the electricity is turned off, the wires and connections cool down and contract. All the expanding and contracting will eventually open up a gap, exposing the wire to air. The resulting oxidization causes the connection point to get even hotter
The International Association of Certified Home Inspectors has some great information on aluminum wiring. They state that aluminum possesses certain qualities that, when compared with copper, make it an unfavourable material as an electrical conductor. These qualities will lead to dangerous, loose connections, as mentioned above, with fire hazards becoming more likely. Some of these qualities are:
Higher electrical resistance: Aluminum has a high resistance to electrical current flow. Therefore, given the same amperage, aluminum conductors need to have a larger diameter than copper conductors.
Less ductile: Aluminum will wear and break down more readily when subjected to bending and other forms of abuse than copper, which is more pliable. Wear, over time, causes the wire to break down internally and will progressively resist electrical current, causing a build-up of excessive heat.
Galvanic corrosion: In there is moisture present, aluminum in homes will experience galvanic corrosion when it makes contact with certain dissimilar metals.
Oxidation: The outer surface of the wire will deteriorate when exposed to oxygen. This is known as oxidation. Aluminum wire oxidizes more easily than copper wire, and the compound formed by oxidation – aluminum oxide – is less conductive than copper oxide. Over time, oxidation can deteriorate connections and present an increased fire hazard.
Greater malleability: Aluminum is soft and malleable, so it is extremely sensitive to compression. If a screw is over-tightened on aluminum wiring, for example, the wire will continue to deform or “flow” even after the screw has stopped being tightened. This can create a loose connection and increase electrical resistance in that spot.
Greater thermal expansion and contraction: Aluminum expands and contracts with changes in temperature more than copper does. As time passes, this will cause connections to degrade. Consequently, aluminum wires should never be inserted into the “stab,” “bayonet” or “push-in” type terminations on the back of several light switches and outlets. Aluminum wiring is safer with screw-type connections, that is, where the electrical wire is wrapped around a screw and kept in place by the head of the screw instead of being pushed in through the back.
Excessive vibration: Electrical current causes vibrations when passing through wiring. The vibrating is greater in aluminum than it is in copper, and, over time, can cause connections to loosen.
What should you do when something goes wrong?
In some cases, copper and aluminum wiring in houses have been combined over the years. This can pose an extreme hazard unless all the proper aluminum-to-copper connectors have been used. Because of the different degrees of expansion and contractions, gaps can occur, causing serious fire concerns.
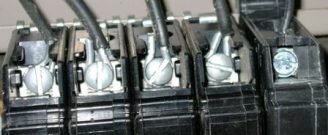
Dangerous Things Your Electrician Wants You to Stop Doing ASAP
Electrical fires are the third leading cause of home structure fires, according to The Electrical Safety Foundation International. Fortunately, there are a variety of preventative measures you can take to help make sure that one doesn’t happen to you.
In addition to having your place’s electrical system thoroughly inspected by a qualified electrician to verify that all electrical work meets safety regulations, electricians say that switching up certain daily habits can help. We asked the pros for some of the most dangerous things you could be doing in terms of your house’s electrics.
Using adapters on two-prong outlets
Because many new appliances—computers, blenders, and more—use three prongs, you might be tempted to nab adapters. Don’t do it, says: “Instead, you should consider upgrading the outlet if you need to regularly use three-prong plugs.”
Plugging in to loose electrical outlets
Loose electrical outlets aren’t safe for kids or pets, and can potentially even lead to fires, says, vice president of operations, a Neighborly company. “If the cord falls out easily, this means that the blades inside the outlet have become loose and can now generate a lot of heat,” he explains.
Not getting old wiring checked out
“Electrical wiring is meant to last 30 to 40 years,” says. “If you move into an old home, old wiring can be a potential danger.” If you think your home may have some, suggests having an electrician survey the wiring to recommend next steps. Rewiring your home can be an unexpected expense, but it will ensure that your house is safer and up to current codes.
Automotive Wiring: Basic Tips, Tricks & Tools for Wiring Your Vehicle
This chart can be used to determine proper wire gauge. First, figure out the amperage of your electrical component. Next, measure the required length of your wire. Then just plug those numbers into this chart to determine the proper gauge.
Cars are filled with stuff that can make or break performance. The engine needs to be fed the proper amounts of air, fuel, and spark. The suspension and brakes must be in tip-top shape. The wheels and tires, transmission, cooling system, gauges—even the seats—must all function properly.
With all those things to worry about, many enthusiasts overlook the electrical wiring system. A lousy wiring job will keep your electrical accessories from operating at full potential—and that means subpar performance.
Round Up The Right Tools
The proper tools will make your wiring job a whole lot easier. Start with a quality set of wire strippers. Wire strippers generally include a group of holes to fit most wire gauges. This allows you to strip the insulation off your wires without accidentally cutting into the wire conductors.
Here are some other items that should be in your electrical toolbox:
A wire brush for removing heavy corrosion, oil, or grease before soldering
A volt/ohm meter to measure voltage and resistance levels in your circuits
A test light to test for power within a circuit
Shrink tubing to insulate connections from outside elements. The tubing slides over the connector or solder joint and permanently shrinks when heated